小米汽车偷工减料?看专家如何回应质疑
随着小米汽车从官宣到产品正式发布、上市,让车市感受到了何为破天的流量,也使得汽车线束这一常被忽视的关键部件受到了广泛的关注。
近日以来,关于小米汽车充电线束将传统的铜材料改为了铝材料,引起了人们的广泛关注和热议。虽然小米汽车官方表示这一做法是行业的正常发展趋势,但部分网友仍对此有所质疑,认为这是“偷工减料”的行为。
图片来源于网络,如有侵权,请联系删除
为深入了解当前行业的最新发展态势,盖世汽车特地邀请了莱尼中国的高级产品经理陆晓广先生以及沪光产品开发中心的总监吴剑先生,共同探讨汽车、智能化演进过程中,汽车线束究竟该如何发展。
图片来源于网络,如有侵权,请联系删除
减重,仍需被放大来看
汽车线束,通常被认为是一辆车的中枢神经系统,其将车载电脑与车辆上的各项相关功能连接在了一起。
图片来源于网络,如有侵权,请联系删除
现阶段,传统燃油车线束均采用铜合金导线,线径的使用由0.35~25mm,每辆汽车的导线使用如果首尾相连约2KM。以一辆B级轿车的重量来估算,导线的重量约25~30KG,汽车每行驶100KM,车辆将消耗近0.1kg的汽油。
如此重量,约占汽车总重量1%~2%,其中75%~80%为导线,端子及接插件占15%,剩下10%为外包材料等。
而值得注意的是,伴随汽车“油转电”,高压部件大幅增加,高载流量势必需要横截面更粗的铜线来实现。在此背景下,如果是一台1.6-2吨重的B级纯电动车,“即便智能化不高,它的整车线束使用量都将达到4km,重量约在60-80kg,占整车重量约在3%-5%。”高级总监 王显斌指出,这一数量还将伴随电子设备数量的多寡上下浮动。
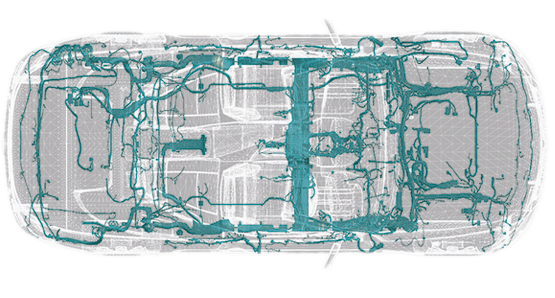
图片来源:莱尼
简而言之,在汽车电气化、智能化甚至是高压化演进过程中,汽车线束的导线正变得越来越长,且横截面更粗,重量势必水涨船高。
正因如此,在动力电池技术尚未得到颠覆性变革,以及汽车E/E架构尚处在域控制器渗透率较低的背景下,通过更导线材质来实现线束自身重量的优化,正成为汽车产业变革过程中的重要措施之一。
铜改铝,SU7真的不是第一例
“虽然大家对‘铜改铝’讨论非常热,但从汽车线缆行业发展来讲,这项技术早已成熟。”陆晓广透露道,作为一家专注于汽车线缆的百年企业,一直以来秉持着TPM战略思路,即技术-产品-市场。当下市场纷纷扰扰,归根结底性价比仍是第一要义。
不可否认,铜芯导线是目前可知的导电率、安全性表现上较为出色的导体,但自2005年以来,铜价飙升,铝作为最有可能取代铜的导体再次被摆上了台面。
单就现阶段来看,“铜的市场售价为每吨7.5万元,而铝仅需每吨2万元,铜的原材料价格就较铝贵了3.7倍。”陆晓广介绍道,“仅看导体,如果用铝代替铜,将大概节省6~7倍成本。”
成本优势突显,其他表现又如何呢?
“相同体积下,铜较铝约重3.3倍,导电性能是铝的1.7倍。如果是相同质量下,铝的体积是铜的3.3倍,导电性能是铜的2倍。”陆晓广分析认为,“基于电阻相同或是载流能力相同,铜的质量是铝的2倍。”
此外,从安装成本角度考虑,由于铝导线相对较轻,其在安装过程中,不需要桥架及穿管,可以节约大量的安装材料,相比铜导线节省20%-50%的安装成本。
正因如此,承载电流大、线径粗,端子和导线拉拔力强的电源线,成为铝导线代替铜导线的主要方案被越来越多企业所接受。换言之,便是小米SU7并不是业内第一例,而是经过了包括特斯拉、比亚迪等一众车企验证过的较为成熟的方案。
而针对由于抗拉强度较低而带来的端子压接拉脱力弱及其他隐性问题,吴剑坚持,在铝线设计、制造工艺及试验规范等方面,沪光拥有多年的研究和积累,在小平方铝线、大平方铝线、铝排以及铝导线适用的端子铜铝链接等多方面均有研究,并已完成多项专利申请。
图片来源:沪光股份
他进一步表示,“材料的切换,并非简单地基于成本考虑,而是涉及多方面的因素,包括性能、安全、成本及技术发展趋势。也不是大家理解的简单替代,是经过了一系列严格的产品设计、零件试验以及车辆路试验证,其中包括了强化耐久等相关试验,以确保车辆的性能和安全不受影响。”
回归小米SU7,其目前话题重点在充电枪等局部应用上,而非100%全车应用,“这也是车企在权衡成本、重量与性能等多层面后的一个综合选择。”王显斌如是说。
智能电动车时代,线束还待变化
如果说,去年是汽车NOA落地元年,那么今年便是各大智能汽车城市NOA规模化落地的关键期。体现到整车上,便是感知层、决策层及执行层等相关部件的堆积。
根据泰科电子官网,为了实现更智能的座舱交互、更高水平的自动驾驶、更低延迟的,汽车高速连接器的传输速率要求有望从150Mbps(车辆状况报告、普通IVI系统等功能)逐渐提升至24Gbps(L3~L4级别ADAS、先进IVI系统等功能)。随着智能化程度的提高,FAKRA、Mini-FAKRA、HSD、车载以太网连接器等高速连接器的应用场景将更加丰富,不同高速连接器将按照传输速率与频率的不同在车内各个领域得以应用。
“高速通讯相关线束对产品的精度、一致性要求已不是传统的线束制造可以满足的了。”吴剑分析指出,从选材上来看,将优选高质量、高性能的材料和连接器,以确保信号传输的稳定性和可靠性。同时通过优化线束的布局,缩短感知系统和模块中间的那些距离,还要做一些必要的屏蔽设计,减少电磁干扰。此外,需进一步提升制造环节的可靠性、稳定性以及可追溯性。
感知层的通讯只是其一。作为智能驾驶时代执行层的关键——底盘,正通过线控改造实现“人机解耦”:将驾驶员的操作命令通过电子控制器传输给执行机构,替代方向盘、踏板等传统机械连接,因而具备了高精度、高安全性、高响应速度等优势。
图片来源:莱尼
陆晓广介绍道,以转向为例,传统机械转向仅需要一个2芯的低频线束来传输轮速信号,但进入线控时代,结构将变得更加复杂,需要4芯甚至多芯,且考虑通讯的稳定性及抗干扰性,需转为数据线缆,来保证信号完整性、电磁兼容性等多方面需求。
而以上种种,都在提示人们,智能化程度越高,对线束要求也将越严苛,随之而来的将是成本、成本还是成本。
相较于智能驾驶对线束的颠覆,电力系统对线束的影响并未抵达尽头。例如,去年开启交付的Cybertruck上,特斯拉已自主研发85%控制器,并将在下一代平台中,完成对“老旧”控制器的全部升级,全部转向48V电力系统。
从技术本身来看,电压由12V升级到48V,高了四倍,理论上通过的电流就会更小,能够减少传递过程中的损耗,并降低温度,同时还能减少对线材直径的需求。而更细的电线意味着更少的材料,就能降低线束的重量,从而降低成本。
图片来源:莱尼
“尽管目前48V系统在整车上已有一些应用,但更多是在一些大功率回路上,如果将整车电网都切换为48V,将对整车线束截面积有着巨大变化,这将可能推动整个汽车电气系统的升级甚至是迭代。”吴剑如是说。
毫无疑问,汽车线束是最容易被忽略的安全部件。但随着汽车电气化、智能化的高速发展,线束变得至关重要。因此,他认为,是时候打破陈规,让线束供应商更早地参与到整车线束规划设计中去。这样才能更系统地提出轻量化、更完整且更精确的解决方案。
本文 zblog模板 原创,转载保留链接!网址:https://qxj.scgwwc.com/post/442.html
1.本站遵循行业规范,任何转载的稿件都会明确标注作者和来源;2.本站的原创文章,请转载时务必注明文章作者和来源,不尊重原创的行为我们将追究责任;3.作者投稿可能会经我们编辑修改或补充。